The wood for our foldable box
The main material of the FridayBOX is plywood, often also called multiplex – a fantastic material for our foldable boxes that can be made from different types of trees.
But not every type of plywood is suitable for the FridayBOX: poplar, for example, is too splintery and beech panels are often badly warped. We therefore manufacture the FridayBOX from shiny, mostly light-colored European birch. This is a great wood, also concerning the technical features.

Wood & linseed oil
A powerful duo from nature
The FridayBOX is treated with linseed oil. Linseed oil is used to protect wood for centuries. It is absorbed deep into the wood and hardenes over time. The wood structure stays ‘open’ but is protected from moisture anyhow. We add a bit of orange oil, that accelerates the drying.
This protection can be reinforced or renewed by anyone if necessary. Just put a bit of linseed oil on a cotton tissue and add a thin layer of oil to the FridayBOX.
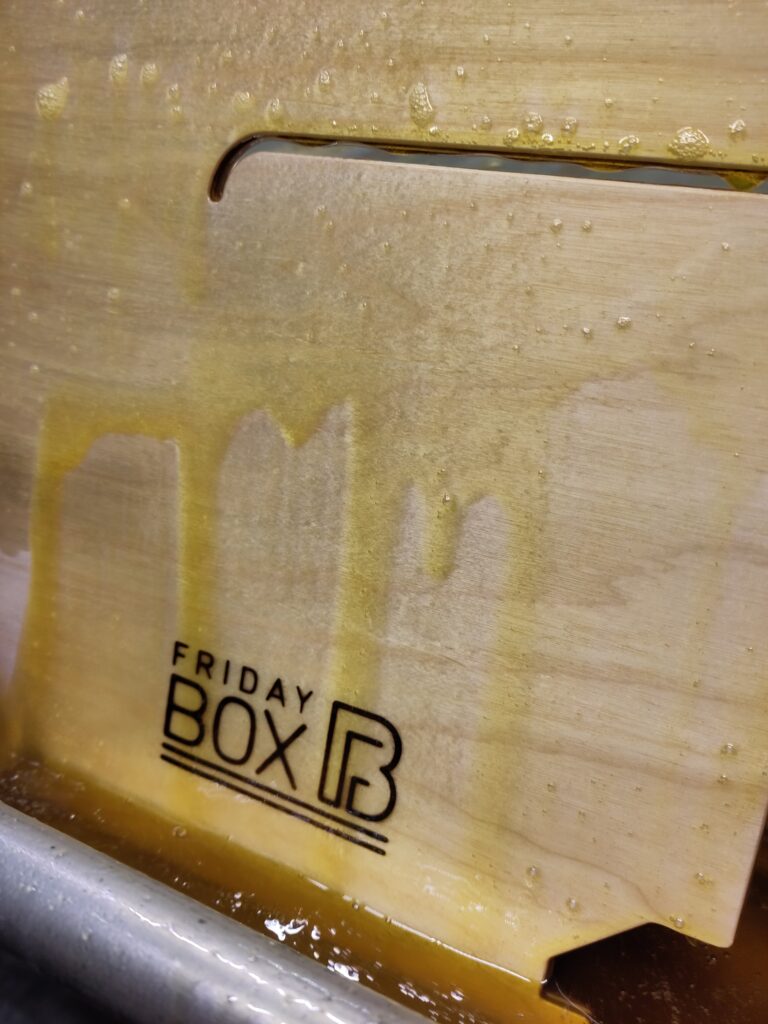
Detailed Dimensions of our FridayBOX
The BIG one
External dimensions
Erected 400 x 600 x 245 mm Height in stack 241 mm
Folded up
400 x 600 x 33mm
Height in stack 29mm
Internal dimensions
370 x 558 x 235 mm
Weight 3kg +/- 0.2 kg
Volume ca. 48 litre
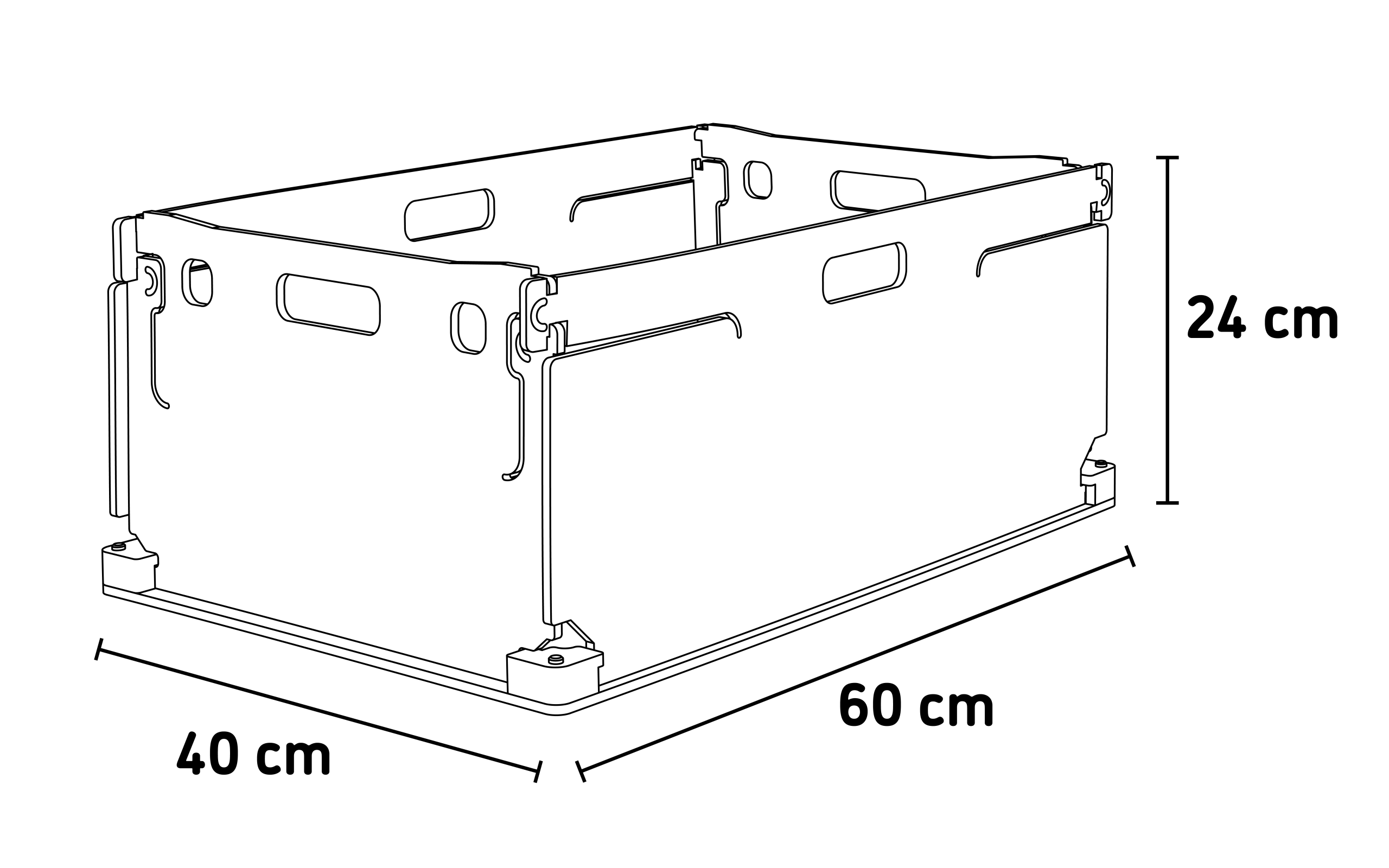
The SMALL one
Outer dimensions
Erected 350 x 490 x 235 mm Height in stack 231 mm
Folded up
350 x 490 x 33mm
Height in stack 29 mm
Internal dimensions
320 x 448 x 225 mm
Weight 2.3 kg +/- 0.2k
Volume ca. 32 litre
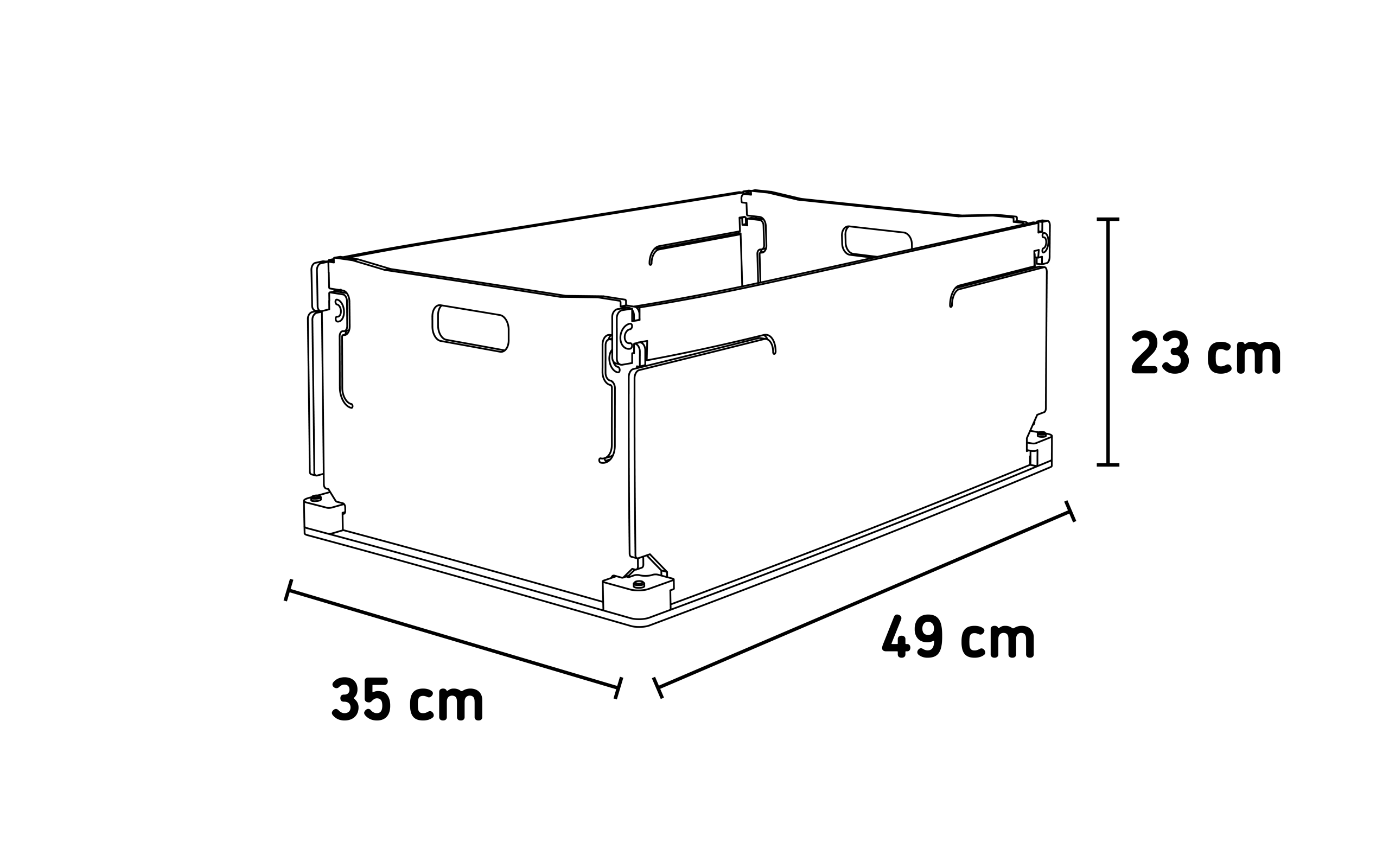
The MINI one
Outer dimensions
Erected 300 x 400 x 191 mm Height in stack 187 mm
folded up
300 x 400 x 33mm
Höhe im Stapel 29 mm
Inner dimensions
270 x 358 x 181 mm
Weight 2,0kg +/- 0,1k
Volume ca. 18 litre
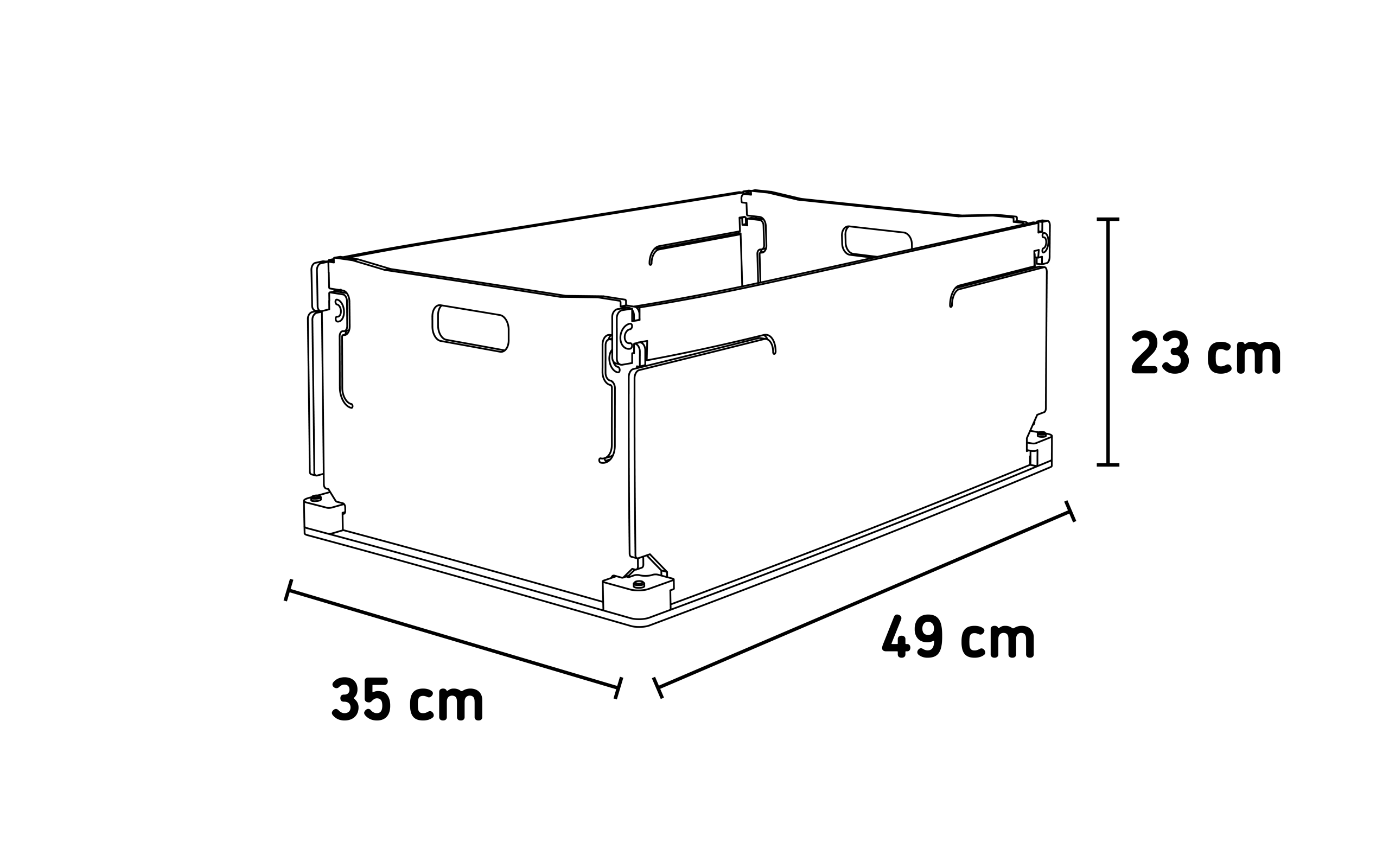

Here is a picture to compare the size of erected wooden boxes and a big box that is folded together to a height of 33 mm.
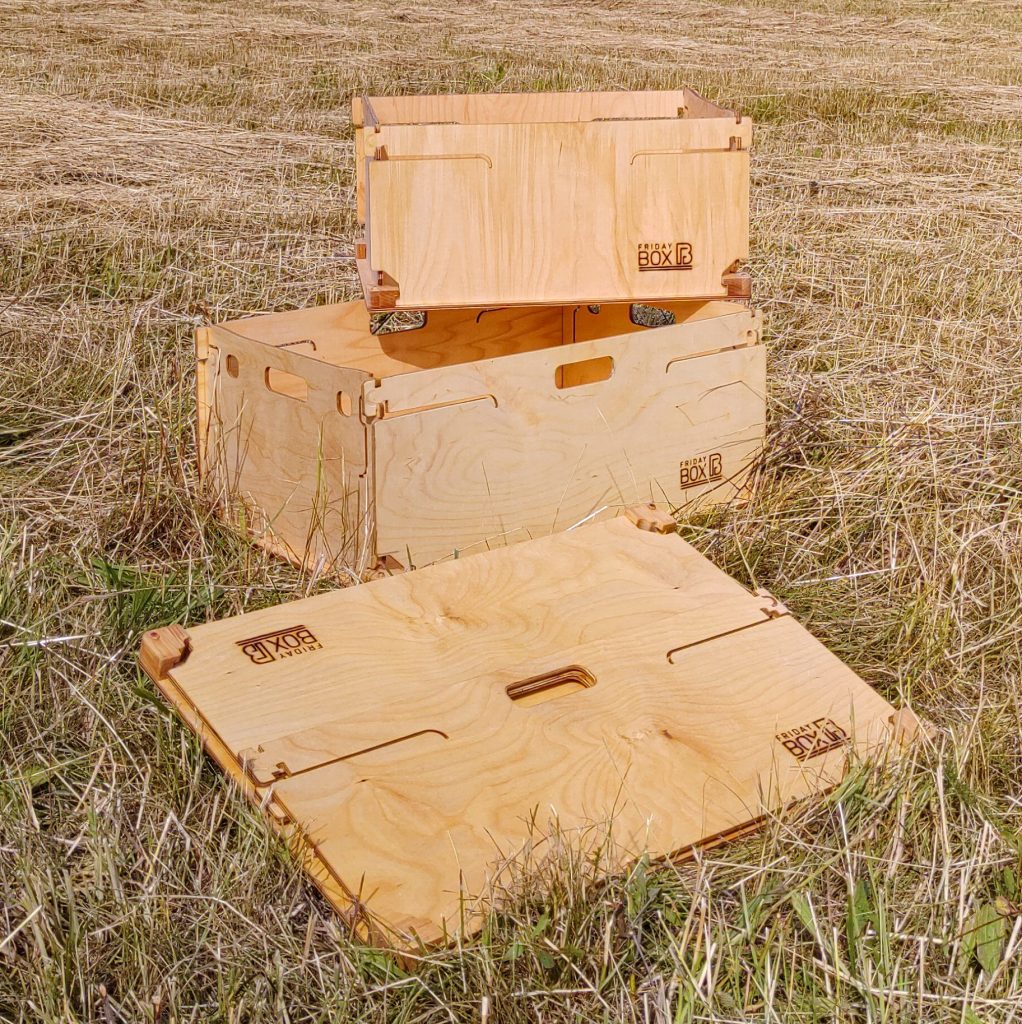
Fastening of the foldable box
The fastening of our foldable wooden box relies on the flexibility of the wood and the proper incisions and geometries, that enables our mechanism withour further fittings or binders.
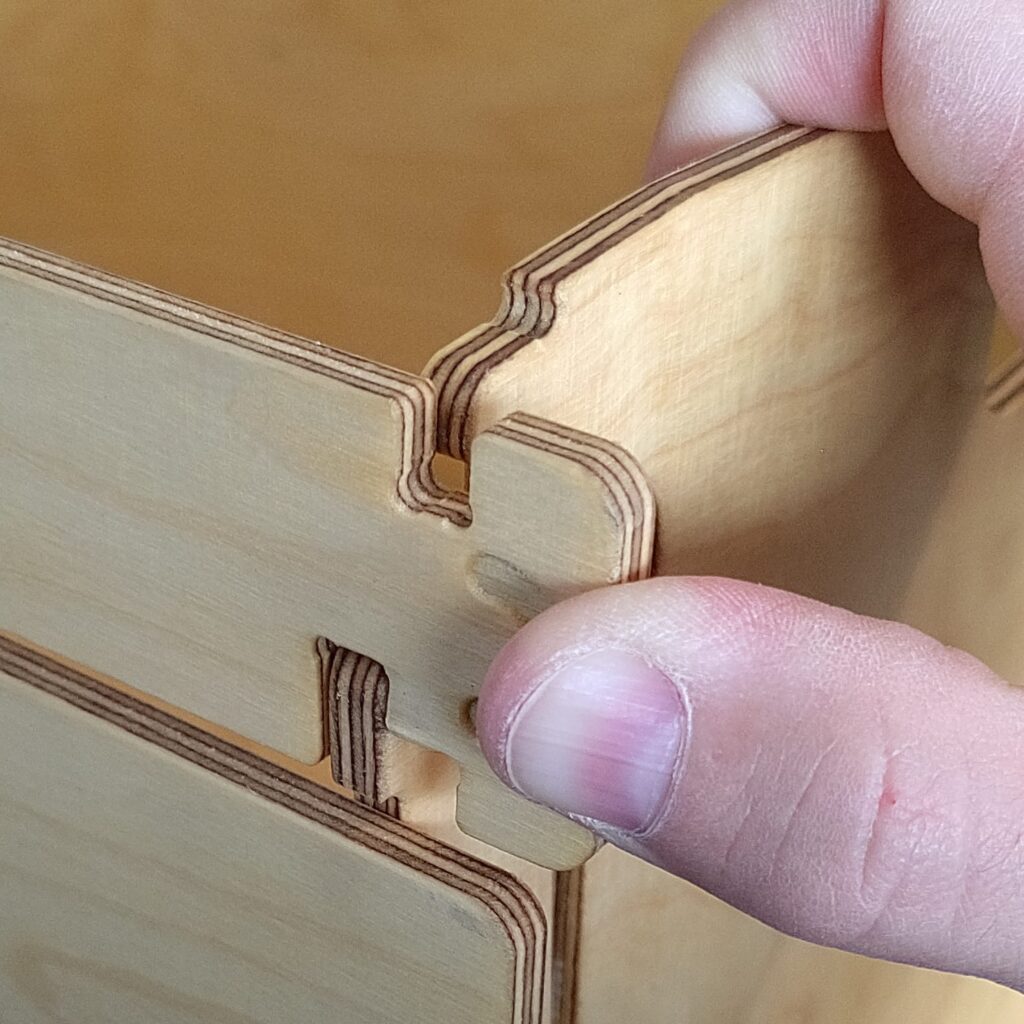
On all four upper corners the mechanism can be easily and quickly snapped into place.
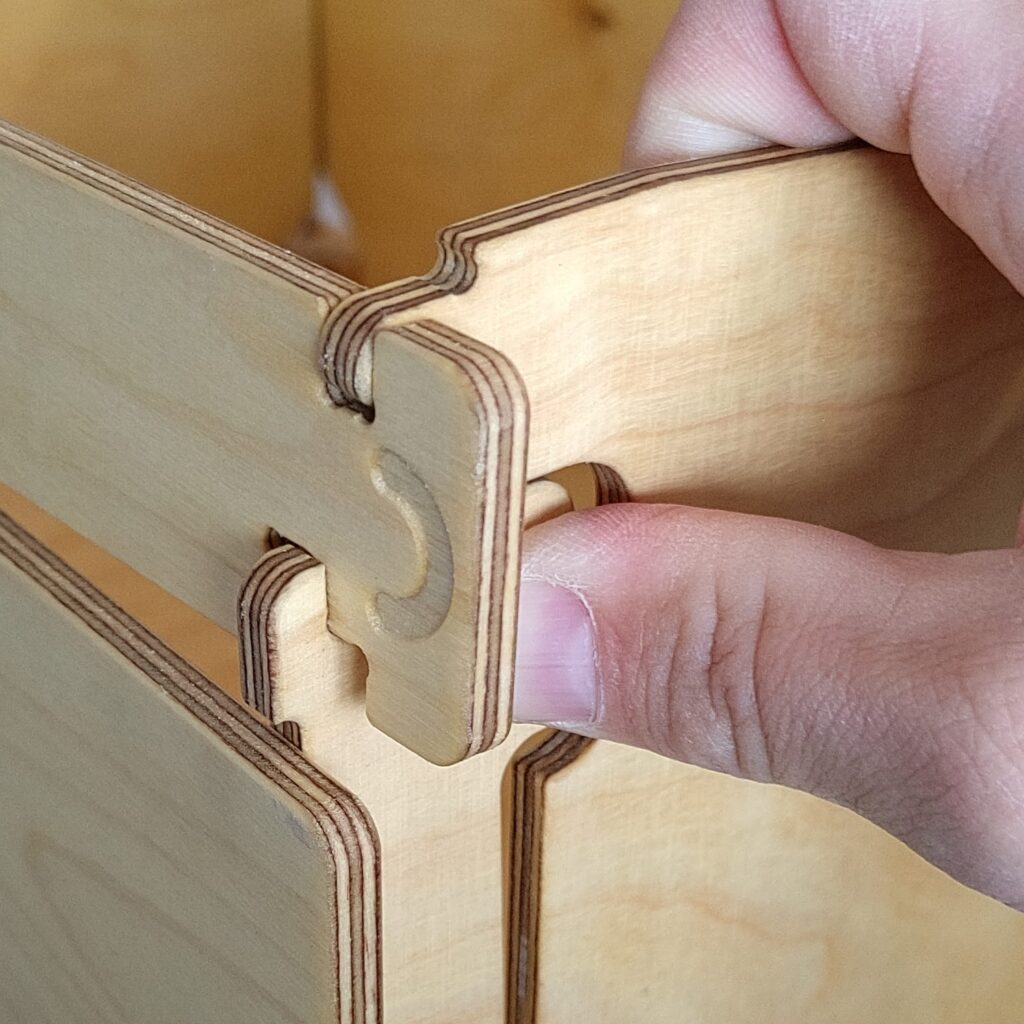
Folding the box is equally quick. Once the fastening is unlocked, the sides fold smoothly together – nearly by themselves.
How high is the folded FridayBOX?
Folded together the FridayBOX is like a hint of nothing: the big one as well as the small one is only 33 mm thin. By being so slim the FridayBOX can be stacked perfectly and particularly space saving when you don’t need it right know. But who owns the box will realize quickly: basically it is nearly never not in use.
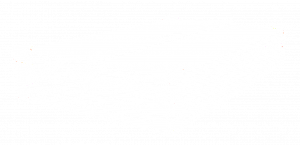
How strong is the FridayBOX?
Laboratory and practical tests show that the FridayBOX is a very stable folding box. The wood is not sensitive to heat and cold as it gets neither brittle nor rough under those exposure. In addition to that our box can be heavily loaded!
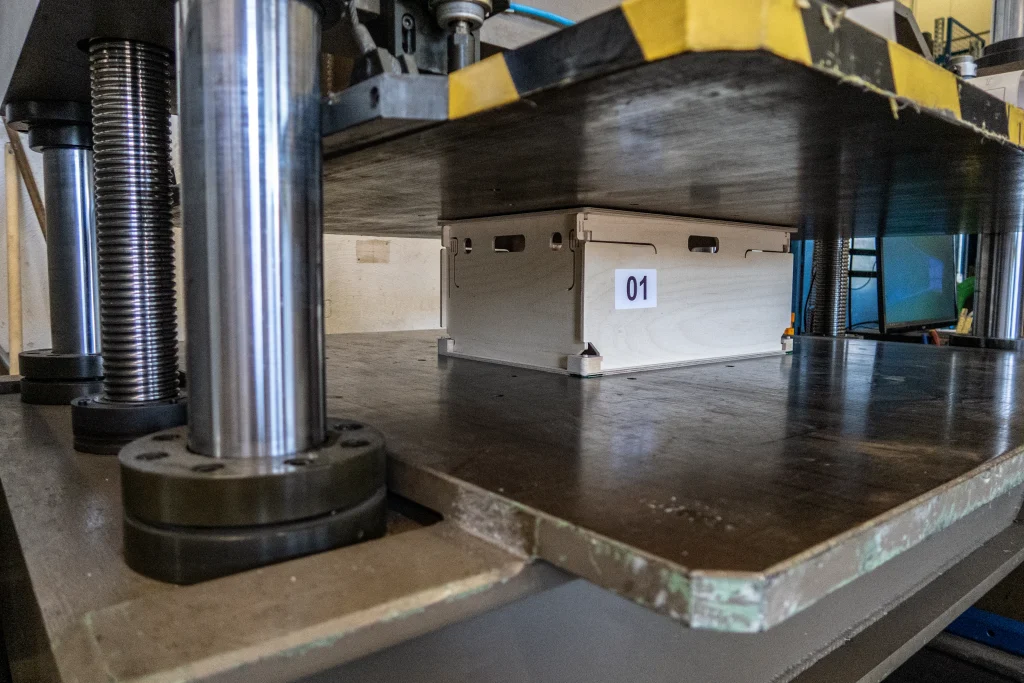
Meanwhile there are more than 1000 FridayBOXes out there in urban and rural wilderness showing customers and us successfully how robust the box is.
The FridayBOX can hold more weight than most of us are able to carry. And sitting on it is more an issue of space as our robust foldable box can support more people than those who can sit on it even when sitting on top of each other.
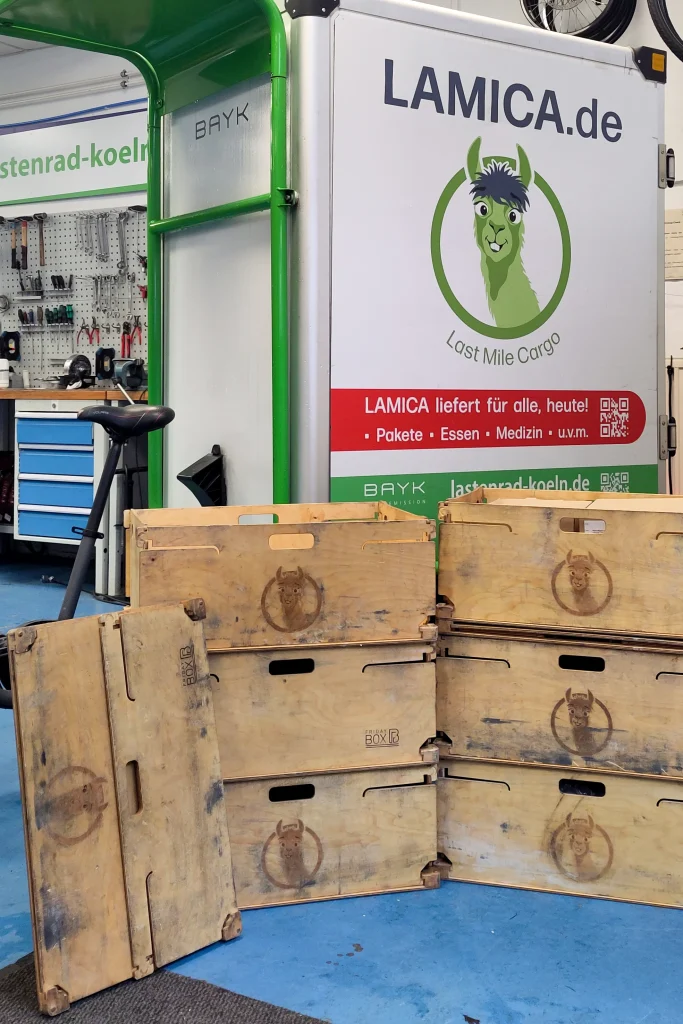
Where is the FridayBOX manufactured?
Home of the FridayBOX is the Rhineland – between Cologne and Dusseldorf. The FridayBOX was and is being (further) developed at the project headquarters in Dormagen, where Michael and his helpers produced the first batches by the end of 2022.
Since January 2023, the FridayBOX is produced on our machines at the Varius Werkstätten, that are part of the Lebenshilfe in the Rhein-Kreis-Neuss . Michael accompanied the start of series production there every day for several weeks, familiarizing his colleagues with the milling machine, technology and software, passing on countless tricks to the experts on site and learning so much himself.
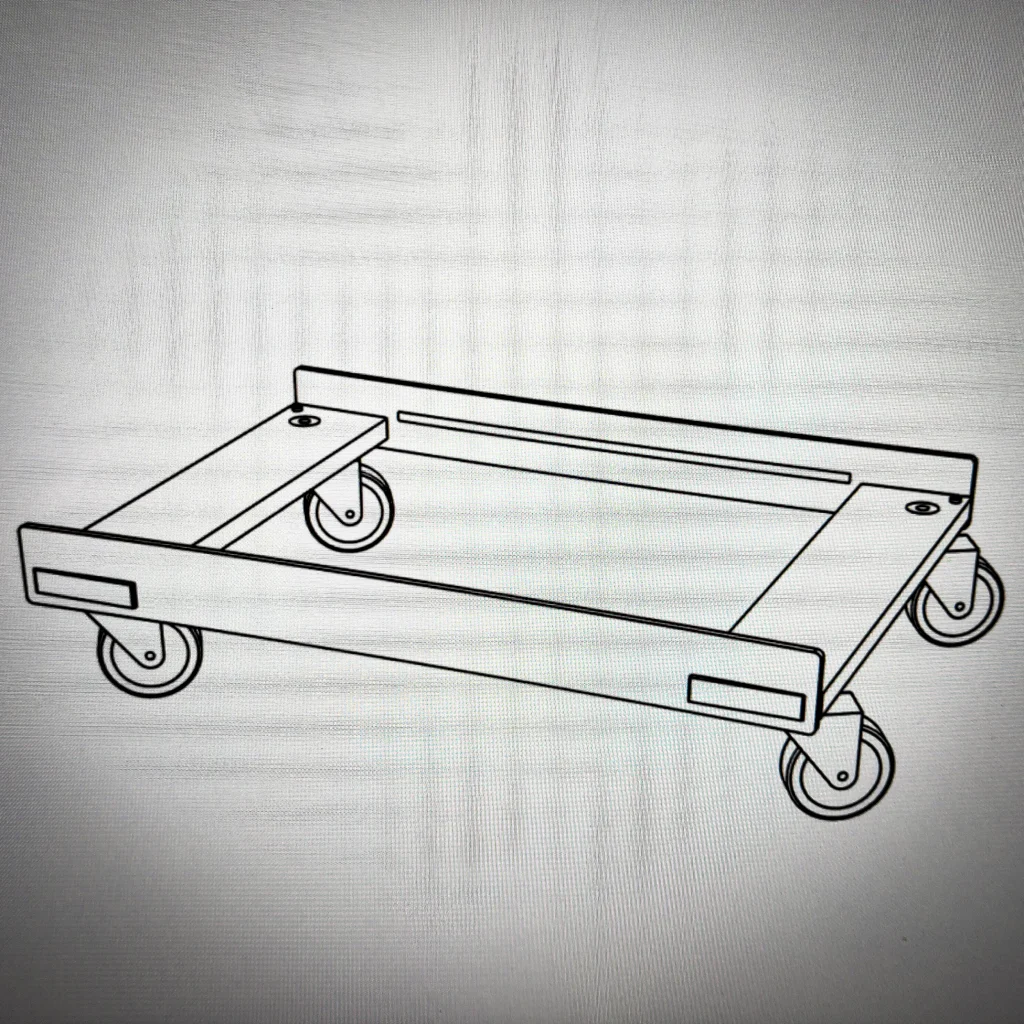